Customer: Textile industry
Description: The company is one of the oldest industries in the textile sector and symbol of excellence of Made in Italy internationally. All phases of fabric transformation aim at higher quality standards and are carried out with maximum sensitivity.
Service: Cloven
Objective: Monitoring and saving energy consumption
A COMPANY WITH A SUSTAINABLE STRUCTURE
The historic Turin-based company bases the quality of its products on the meticulous selection of the best raw materials worldwide.
He applies all his know-how during the production process, to enhance the natural and precious characteristics of the various fabrics, looking with a careful eye towards innovation in terms of performance and design.
Sustainability, especially under the guidance of the 14th generation, has become one of the fundamental pillars to follow and that merges with the core values of the plant. One of the goals was to monitor the various energy consumption to try to mitigate their consumption and costs and lead the company over the years to a more efficient eco-business model.
Trigenia was fundamental to achieve this goal and moved to support it thanks to the installation of an energy monitoring software, a useful tool to keep under control expenses and reduce them.
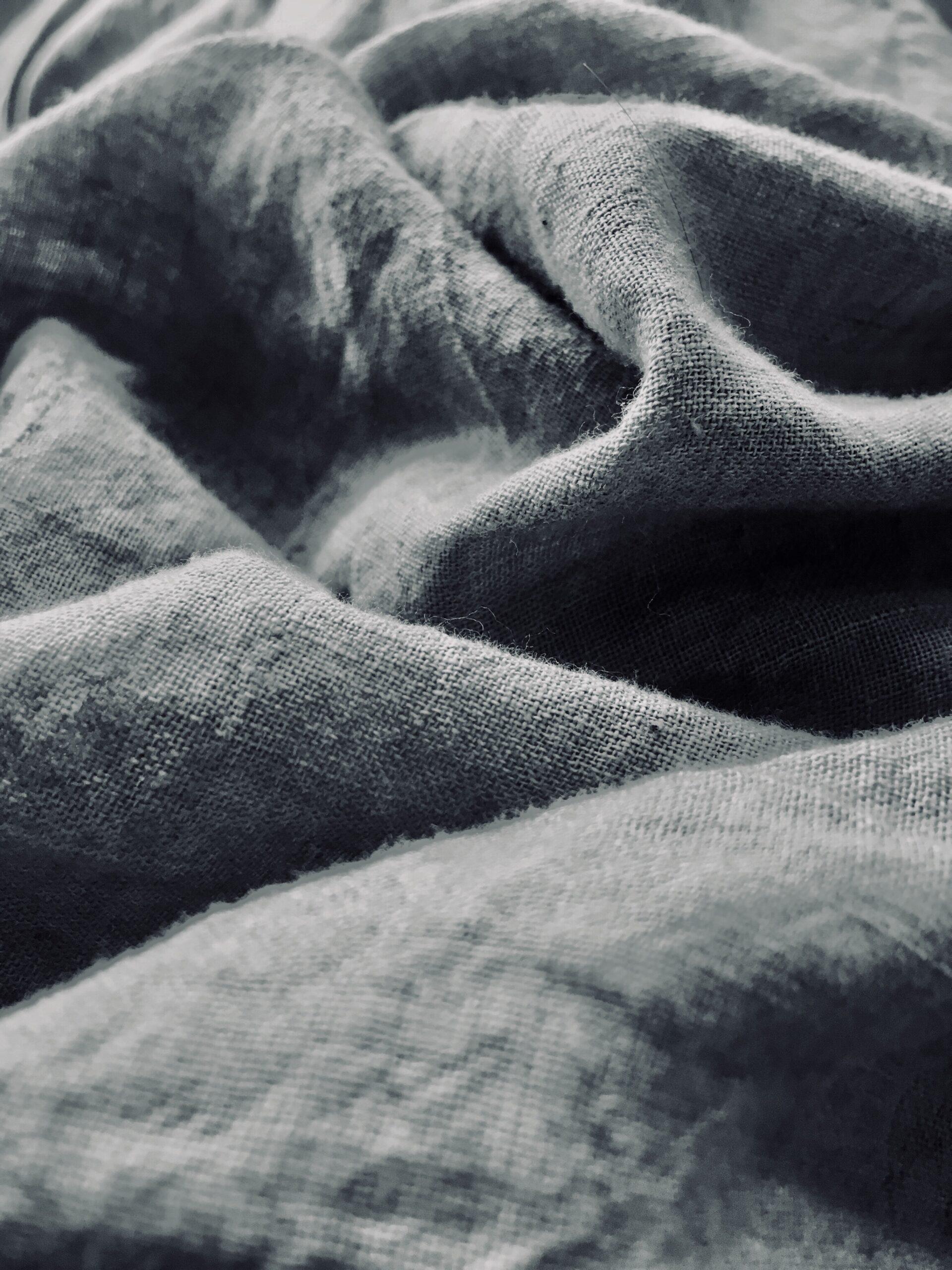
METHODOLOGY
Trigenia gaves support to the company for the installation of an energy monitoring system to collect data on electrical users.
In five years, monitoring has expanded and diversified. There has been the addition, in fact, of several meters with the aim of knowing how the various energy carriers and plants are used within the plant.
To identify areas for energy improvement, the supervision of plants using compressed air, the water cycle within the production process, the cogenerator, as well as thermal energy and natural gas used has been digitized.
As a result of this activity, the monitoring of the compressed air produced by the compressor room led Trigenia to implement in an EPC project to carry out the replacement of a low-performance compressor.
RESULTS- ENERGY SAVING AND PROCESS EFFICIENCY
Thanks to this activity a saving of 7% was obtained on the thermal energy carrier.
Request a consultation
We are at your disposal to answer all your doubts.