Description: Leader company in the production of cast iron and steel castings for the machine tool sector for the automotive industry
Service: White Certificates
Objective: Implementation of the savings measurement program; request for access to the White Certificates mechanism and subsequent reporting of savings.
ENERGY EFFICIENCY
Trust and mutual esteem are the fundamental components of the relationship that since 2017 has bound Trigenia to a leading company in the steel and metallurgy sector.
Founded in 1967 the foundry has been able to evolve to occupy a role of primary importance in the production of molds for the body shop of the international automotive industry.
Trigenia has supported the company in the process of transformation and change towards more sustainable energy models, sharing the most difficult challenge: identifying and managing the main “critical points” energy consumption of the Company and transform them into strengths in terms of energy efficiency.
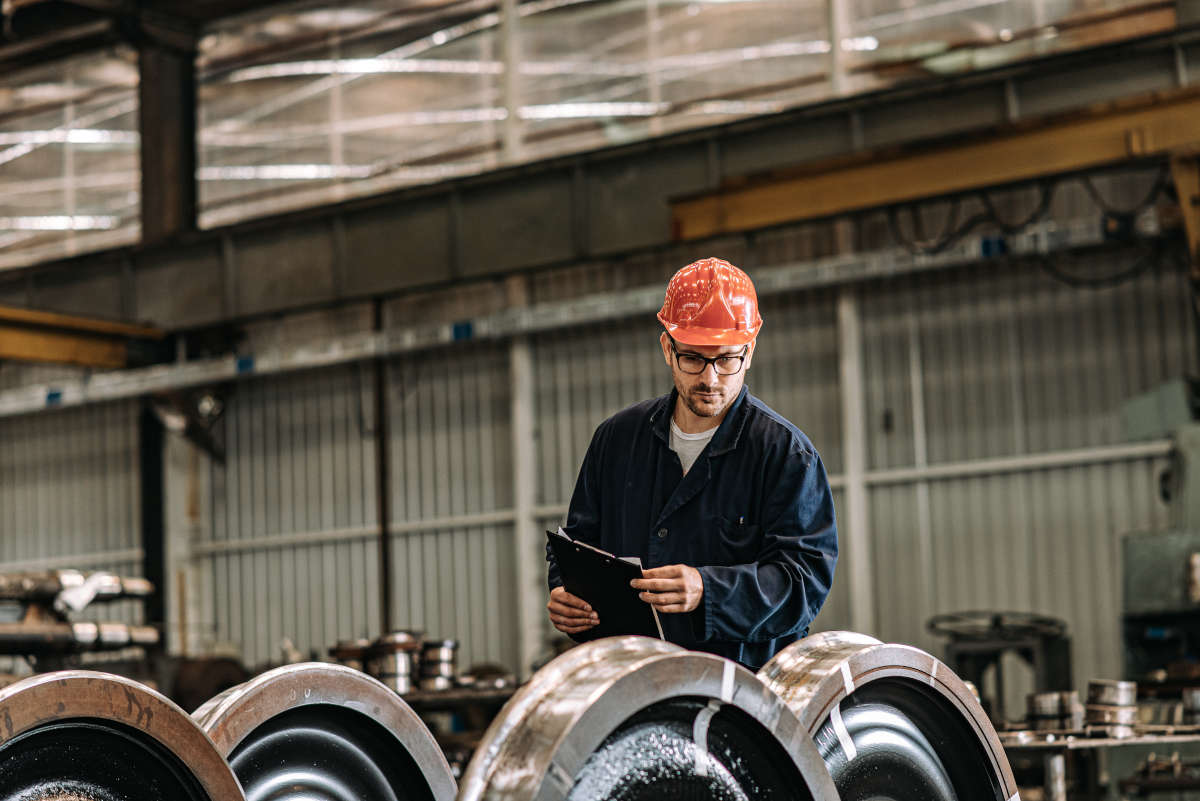
Trigenia was responsible for the implementation of the savings measurement program, the request for access to the White Certificates mechanism and the subsequent reporting of savings, obtained thanks to the installation of two electrical energy monitoring systems that provide for the detection of:
- Electricity absorbed by melting furnaces
- Gross production of melting furnaces
After the replacement of the furnaces, with medium frequency, high efficiency crucible induction melting furnaces, the company recorded:
- An important energy saving related to the efficiency of the cast iron casting process obtained thanks to the increase in frequency to 250 Hz
- The possibility of switching off the oven between two separate productions
- A reduced maintenance period of the molten metal until total emptying by tapping of the furnace
- Savings of about 300 toe/year of electricity
- Annual issuance of 1,000 Energy Efficiency Certificates (TEE) Type I (Electricity Savings)
Request a consultation
We are at your disposal to answer all your doubts.